От Производства-Под-Зарплату к Производству-Под-Заказ
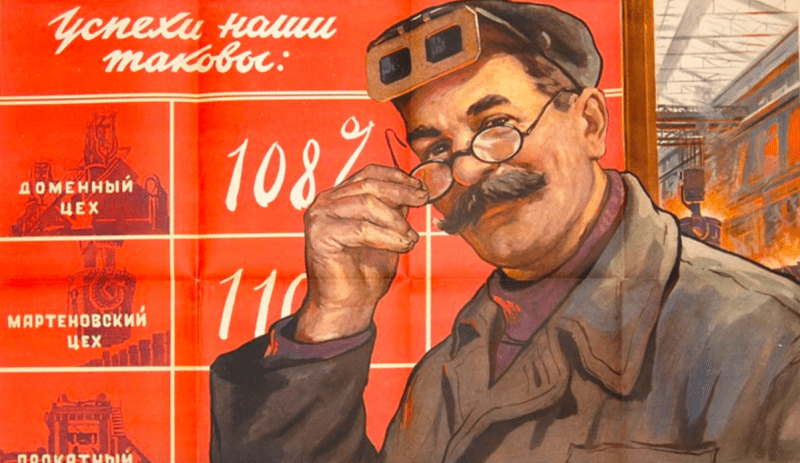
Постановка задачи
Теоретики и некоторые практики производственного консалтинга хорошо знают западную классификацию типов производств (предприятий) в отношении главной цели бизнеса – удовлетворения клиентского спроса.
Это: «разработка-под-заказ», «производство-на склад», «производство-под-заказ», «сборка-под-заказ».
Не так давно, после особо эмоционального общения с производственниками одного из российских заводов, работающего, вообще говоря, «под заказ», но реально — совсем нет, в результате дискуссии, я бросил: «…у вас же сейчас производство-под-зарплату..».
После, обдумав этот новый классификатор производства, я с сожалением сделал вывод: да, очень многие наши (прежде всего говорю про машиностроительные и приборостроительные производственные компании) производства работают по типу «производство-под-зарплату».
Основные характеристики, по которым предприятие можно отнести к этому типу:
- сдельная оплата труда, зависящая от закрытых (принятые детали) нормо-часах в месяц;
- месячный цеховой план к выполнению, кроме номенклатурного – в нормо-часах;
- превышение плана производства возможностей цехов.
Производствами, работающими «под-зарплату» в реальности управляют простые рабочие, иногда – мастера. Каждый день они сначала «делают» себе зарплату, т. е. делают наиболее выгодные по соотношению «реальное время производства и размер партии / трудоемкость операции» детали, затем, в оставшееся (если таковое есть) время — детали «под заказ».
Что имеем в итоге
- на сборке – всегда дефициты, при этом склады сборочных цехов или деталеделательных (или — склады ПДО, готовых деталей и т. п.) — завалены тем, что не нужно в данный момент, месяц, квартал, год;
- выполнение номенклатурного плана цехами – не более 80%. Но при этом (!)…
- … выполнение месячных планов по трудозатратам (нормо-часам) — всегда 100±1%;
- управление производством выполняется в режиме редких (раз в день) или частых (несколько раз в день) планерок. Директор по производству, а иногда и генеральный директор, минимум 30% своего времени, а в конце квартала/года — под 80% работают главными диспетчерами.
С точки зрения Lean все это – сплошные, весьма очевидные и крайне тяжелые для экономики предприятия потери: проталкивание вместо вытягивания, причем даже не под прогноз / план, а под плановые абстрактные нормо-часы (зарплату), перепроизводство, производство не вовремя, и т. п. С точки зрения начала Lean или любых преобразований это то, с чего надо начинать! Именно здесь, с точки зрения системы Тойота «точно вовремя» — самый близкий к поверхности «подводный камень», мешающий уменьшению уровня запасов, а следовательно – увеличению пропускной способности (по ТОС). А это не просто важно – смертельно, для перегруженных, растущих производств.
Зачем, скажите, ставить 5С (система организации и рационализации рабочего места), стандартные операции, SMED (быстрая переналадка оборудования) — если результатом будет лишь более эффективное и удобное производство незавершенки (НзП)? Как, скажите, с помощью канбан ограничить / спланировать запуск производства, если рабочий получает за «нормо-часы», а не за закрытое количество канбан? И если канбан не будет – он все равно будет точить детали?
Но, по практике известных мне большинства проектов Lean, это как раз то, с чего как консультанты, так и предприятия никогда не начинают. Почему? Сложно! Реально – это Авгиевы конюшни №2 (№1 – постановка системы управления электронным составом изделия).
Чем обычно ограничиваются консультанты: рекомендуют перейти на повременную систему оплаты, заставить сдавать цеха комплектно и пр. Хорошие советы, но из серии «вам надо стать ежиками». Как их применить? На заводах, в большинстве своем либо знают, либо догадываются о том, что «сделка», как сигареты — «вредит Вашему здоровью» или даже «убивает».
Но как этого уйти? Платить повременно – рабочие перестанут работать. Платить за выполнение номенклатурного плана? А если в плане деталей нет, а делать надо? Не попала деталь в месяц, конструктор / технолог не вовремя провел изменение, или ДЕФИЦИТ НА СБОРКЕ («… надо очень – очень аварийно Иван Иванович!!!…»). И как платить рабочему его привычную месячную зарплату, без которой он просто уйдет – и дефицит квалифицированных рабочих рук просто так заполнить будет нечем? И т. д., и т. п.
Это — неудобные и непростые вопросы. И отсутствие понимания (консультантов) проблемы, что делать, как делать, и, с другой стороны, отсутствие воли руководства завода «будем делать», приводят к возникновению производств вот такого нового, уникального типа. «Производство-под-зарплату», не «под-заказ» и даже не «на-склад».
По моему глубокому убеждению, для подавляющего числа российских заводов, в особенности — крупных, старой формации, именно с решения этого вопроса надо начинать построение Производственных Систем.
Необходимо строить, прежде всего, систему планирования и управления производством, обеспечивающую:
- понятный всем (вплоть до рабочего у станка) план того, что нужно сделать за период;
- сбор факта, с которым не поспоришь и не представишь так, как выгодно;
- мониторинг происходящего в рамках периода для своевременного оказания управленческих воздействий.
На основе системы и можно будет, но очень поэтапно и осторожно, начинать уход со сделки. Придя, в итоге, к позаказному производству «Точно Вовремя».
Замечу, что Lean методы и инструменты здесь вполне применимы. Вот только применять их нужно не для построения «бережливого производства» — предприятие, «внедрившее» «Lean», но работающее в явной или скрытой форме «под-зарплату», а таких у нас уже немало – это абсурд!
Этапы перехода
Предлагаемый и описываемый ниже путь от «сделки» есть переход на окладно-премиальную систему. Оклад — за квалификацию, премия – за исполнение плана производства. С одновременным изменением мотивации рабочих на «производство-под-заказ», начиная с заготовительно-штамповочных переделов. Замечу, что уход от «сделки» — не самоцель, но необходимое условие для перехода на позаказное, синхронизированное с заказами (контрактами) планирование и управление производством и закупками. Что для наших заводов неизбежно, т. к. большинством из них управляют КЛИЕНТЫ (заметьте, не ПДО, генеральный или управляющая компания).
Формализация цели
Цель: перевести производство от «производства-под-зарплату» к «производству-под-заказ».
Создать условия, при которых цехам:
- будет выгодно выполнять, прежде всего, номенклатурный позаказный план;
- будет невыгодно не выполнить номенклатурный позаказный план;
- не будет ставиться план в нормо-часах (одна из типичных практик «вредительства» ПЭО на традиционных предприятиях).
Что делать. Концепция и этапы перехода
1. Для цехов должен рассчитываться автоматически план — не предмет переговоров, но предмет «тупого» расчета, номенклатурный позаказный цеховой план производства. Это — задача IT-системы управления производством, которая, замечу, должна быть Lean (т.е. — не ERP/APS/MES). Для каждого цеха план должен иметь следующие характеристики:
- «План выпуска» — какие детали, в каком количестве, к какому числу и в какие цеха должны быть поставлены. Это — традиционное требование к планам производственной системы, у многих это есть.
- «План запуска» — какие детали, в каком количестве (без учета консолидированных партий), когда должны быть запущены. А вот это — нетрадиционное требование к системе управления производством на традиционных предприятиях, на которых существует и отслеживается только «план выпуска». Приводит это, в частности к тому, что информация о том, что какие-то детали вовремя не запущены, обнаруживается только на сборке. В результате — дефицит, аварийная ситуация, и пр.
- План (выпуска) виден не на весь горизонт планирования, но только на ограниченный период (окно планирования). Через план выпуска цех видит и может планировать подготовку производства на то, что надо будет делать.
- План (запуска) открыт также на ограниченный период (окно запуска), достаточный для консолидации в партию и одновременного запуска одной детали на несколько заказов. Через окно запуска цех может запустить только определенную партию деталей (определенные планом детали) – не более.
2. Устанавливается абсолютно «железное» правило: все детали обязательно перемещаются по участкам / цехам только в сопровождении маршрутной карты (МК). Должен быть установлен принцип с изменением системы контроля качества (если необходимо) и, (необходимо!) принципов учета сделанной продукции / оформления нарядов: «нет МК — нет детали — нет наряда». Следовательно: нет наряда — нет зачета выработки — нет зарплаты. Практика показывает, что сделать это не так уж и сложно. МК формируются только из ИТ-системы управления производством (рукописные – не принимаются), при запуске, т.е. начале производства детали.
Замечу, что переход на ограниченный запуск, автоматическое (не ручное) формирование МК — есть первый шаг к переходу на вытягивающее планирование и управление производственным потоком по электронному канбан.
3. Цеху-поставщику «засчитываются» за период только те детали, которые:
- были в плане (выпуска) цеха за период;
- были приняты (оприходованы и не возвращены) цехом-потребителем за период.
4. Система расчета заработной платы модифицируется следующим образом (этап 1):
- ИТР (инженерно-технические работники цеха) получают фиксированную часть заработной платы, по ставкам. Переменная часть автоматически рассчитывается на основании % выполнения плана.
- ОПР цеха получают зарплату почти сдельную, из расчета закрытой трудоемкости, но только для деталей выполненного плана.
5. Резюме. Данная система есть система типа «кнут и пряник»:
- С одной стороны, цеха просто физически не могут запустить «дальние» или просто ненужные детали (детали вне плана), т. к., «правильная» ИТ система управления производством просто не предоставляет информации о том, что цех может сделать вне периода «окно планирования». Соответственно, «нет запуска — нет МК — нет (засчитанной) детали».
- С другой стороны, мотивация направлена именно на выполнение позаказного номенклатурного плана, формируемого системой планирования.
6. Дальнейшее развитие системы оплаты:
- Дифференцированная оплата как ИТР, так и ОПР за ритмичную, в рамках месяца, сдачу деталей потребителю.
Иными словами, разная оплата за «красные», «желтые», «зеленые», «синие» детали. Где «красные» — есть детали, поставленные со срывом срока, «желтые» — «с колес», «зеленые» — вовремя, «синие» — раньше срока. Также, можно ввести «серые» детали (поставленные вне плана зачем-то), «фиолетовые» (поставленные из свободного остатка) и т.п. – фантазия здесь не знает предела.
Для данного варианта система расчета премиальной части может быть, например, такой:
— «серые» детали — не засчитываются;
— «зеленые» и «желтые» сданные детали засчитываются как 100% от закрытых по ним нормо/часов,
— «синие» — 80%,
— «красные» — 10%.
Указанное, кроме всего прочего, очень сильно мотивирует и на комплектную сдачу, но это тема отдельного разговора.
- Переход на «втягивающее планирование», где МК выполняет роль «канбан», карточки, разрешающей и ограничивающей запуск одновременно.
Замечания по переходу. Для того, чтобы смягчить переход на новую схему (простым он не будет в любом случае), можно запустить новую схему параллельно старой. Рассчитывать и начислять — «по-старому», но одновременно выдавать и ИТР и ОПР квитки с указанием, сколько бы они получили «по-новому». Практика показывает, что 6-ти месячного переходного периода достаточно, чтобы перестроить отношение адекватно настроенного персонала, пережить несколько открытых или скрытых забастовок и найти замену недовольным (как правило, бОльшее их число будет среди ИТР, как ни странно).
Пример практической реализации.
Позаказная (помашинная) вытягивающе-проталкивающая система с электронными канбан и ТОС принципами планирования.
Ниже на обобщенном примере реализованных проектов перевода производства на работу под заказ, приводится описание практических шагов построения системы и ее работы. Схема наилучшим образом применима для машино-приборостроительных предприятий.
Начальные действия:
1. Перед «узким местом» сборочных цехов — как правило, это первый цех в линейке сборки изделия, или участок окончательной сборки организуется производственный склад (ПРОСК), если его нет.
Примечание: очень часто на заводах эту функцию выполняет «Склад Готовых Деталей» или «Склад ПДО» или «Центральный Комплектовочный Склад», в который цеха/участки сдают партии деталей. Так вот – лучше его расформировать (хотя бы частично, т.к. полностью это сделать не всегда возможно), перенеся места хранения и комплектации непосредственно на участки сборки – в ПРОСКи. Также, как и расформировать Склады Готовых Деталей на выходе из каждого цеха – убрать лишние запасы, оставив только «буфер» перед «узким местом».
2. В ПРОСКах устанавливается (внедряется) система предварительной комплектации узлов / агрегатов для сборочных участков. Лучше всего – с использованием специальной тары / тележек, сконфигурированных под комплектацию конкретных узлов / агрегатов. Фактически тара будет выполнять функцию канбан, по генерации сигналов обеспечения сборки. Если детали простые и ходовые, вместо тары могут быть установлены стеллажи (в т. ч. – движущиеся) — система «канбан / супермаркет».
3. Определяется «буфер» (он же — количество канбан в обращении) – т.е. на сколько заказов вперед должны быть в ПРОСКе комплекты.
4. Для каждого цеха (участка), работающего на конкретный ПРОСК, устанавливается число заказов / готовых изделий (M), для которых «открыт» к запуску план производства (например – месячная «партия» готовых изделий – 8-10).
5. В «Lean ERP» системе рассчитывается план (номенклатурный, цеховой (участковый), позаказный) – «барабан» по ТОС. На весь горизонт планирования. Но «открывается» для каждого из цехов/участков только для N+М заказов.
После этого этапа уже можно запускать систему. Как она работает:
1. Начальный момент времени – тележка / тара / супермаркет укомплектованы под сборку конкретных узлов/агрегатов для конкретных заказов/финишных изделий.
2. Начало сборки конкретного узла / агрегата заказа / изделия №N — есть факт выдачи комплектации (выкатка тележки, передача контейнера) на сборку. Факт отмечается в системе, как вариант для простоты — с использованием штрих-кодирования.
3. После этого, автоматически, для каждого цеха / участка, поставляющего детали на эту ТС, в системе «открывается» план запуска (или – появляется «электронный канбан») для комплекта деталей для заказа N+M+1.
4. Далее, плановики запускающего цеха/участка:
- либо видят в системе возможность запустить «открывшиеся» для запуска детали и запускают их, либо…
- автоматически, для запускающих участков, без участия плановиков запускающего цеха, печатается канбан – сигнал к запуску (реализация «веревки» по ТОС).
Примечания. При этом, плановики цехов имеют возможность компоновать детали в партии. Но, только под «открытые» под заказы детали и с формированием канбанов на количество заказов в партии. В качестве «канбан» может выступать стандартный сопроводительный документ, как вариант — сопроводительная бирка или маршрутная карта, желательно – со штрих-кодом.
Ниже пример бирки-МК-канбан.
6. Далее, деталь «проталкивается» по всему маршруту по цехам / участкам, с сопровождающей ее МК, которая сопровождает запущенную под заказ / партию заказов деталь, на всем своем цикле жизни, до момента оприходования в ПРОСК цеха-потребителя.
7. Контроль запуска «разрешенных» деталей выполняют плановики ПДО (в дальнейшем — плановики сборочных цехов, отвечающих за конкретные сборки или готовые изделия), в т. ч. с использованием «Lean ERP» системы.
Общая схема работы системы приведена ниже.
Вытягивающее «ограниченное» планирование для «деталеделательных» цехов и принцип формирования МК. МК — канбан — производственное задание. Общая схема
Статус и приоритет канбан (=МК — производственных заданий в производстве), в т. ч. и в процессе производства, может определяться по расширенным ТОС правилам, через сравнение плановой и ожидаемой даты поступления детали в ПРОСк (агрегатно) сборочного цеха / участка (на рисунке — АСЦ)– см. ниже.
По факту выполнения задания – пополнения ПРОСКа, каждый электронный канбан будет иметь свой цветовой статус.
Собрав за период количество сделанных деталей со своими статусами, получаем следующую картину (пример ниже).
Обратите внимание, насколько хорошо пример иллюстрирует реальную ситуацию: большинство деталей сдаются на сборку либо раньше времени (синие и серые), либо позже (красные и белые), тогда как должно быть наоборот: большинство должны составлять желтые и зеленые.
На основании которой и строится система дифференцированной оплаты «сданных нормо-часов» в зависимости от приоритета сданных деталей:
Белый — позиции не выполнены.
Красный – не успел к плановой дате. Оплачиваются с понижающим коэффициентом.
Желтый – «с колес». Успел на пределе. Оплачивается 100%.
Зеленый – вовремя. Сдал вовремя. Оплачивается 100%.
Синий – раньше, чем надо. Сделал намного раньше, чем надо. Зачем? Оплачиваются с понижающим коэффициентом.
Серый – детали вне плана. Не оплачиваются.
Подобная схема оплаты – не бесспорная. Но, в «тяжелых» случаях не просто помогает, а является единственным способом относительно быстро перейти от «Производства-под-зарплату» к «Производству-под-заказ».